Wie Sonnenlicht zu elektrischem Strom wird
"Photovoltaik", das ist eine Zusammensetzung aus dem griechischen Wort für Licht und dem Namen des Physikers Alessandro Volta, der die Batterie erfand. Photovoltaik, das ist die direkte Umwandlung von Sonnenlicht in elektrischen Strom in einer Solarzelle. Und die Sonne liefert der Erde mehr als 219.000 Billionen Kilowattstunden Energie - jedes Jahr und kostenlos. Das sind zig tausend Mal mehr, als alle Menschen dieser Erde heute verbrauchen.
Seit mehr als 50 Jahren besteht inzwischen die Möglichkeit, mit Solarzellen die Kraft der Sonne zu nutzen und aus ihrem Licht elektrischen Strom zu erzeugen. Allerdings lag der Wirkungsgrad der ersten Silizium-Solarzelle von 1953 bei gerade einmal vier Prozent. Dennoch gehen Experten davon aus, dass in 50 Jahren ein Großteil unserer benötigten Strommenge aus Solarzellen stammen wird.
Der moderne Flachbau liegt - fast idyllisch zwischen Feldern und Wiesen - genau auf der deutsch-niederländischen Grenze. Ein Teil von "Solland Solar" liegt im deutschen Aachen, der andere im niederländischen Heerlen. Eine blaue Linie quer durch die Fabrik markiert, wo Deutschland endet und die Niederlande beginnen. Rund 40 Prozent der 400 Mitarbeiter haben einen deutschen Pass, die anderen einen niederländischen. So fließt das Wissen aus beiden Ländern in die Entwicklung und Produktion von Solarzellen.
Die Umwandlung von Sonnenlicht in elektrischen Strom beginnt mit einem Material, das es weltweit in nahezu unbegrenztem Ausmaß gibt: Sand. Quarzsand, um genau zu sein, auch Silizium genannt.´
"Silizium in sauberer Form, daraus werden Waferscheiben produziert und die sind Basismaterial für die Fertigung von einer Solarzelle."
Erklärt Henk Koerselmann, der bei Solland für den reibungslosen Produktionsprozess - und die Betreuung von Journalisten - verantwortlich ist. Diese nur 0,2 Millimeter dicken quadratischen Siliziumplatten werden als Rohmaterial eingekauft und tragen bereits eine kleine Menge Bor in sich. Das Halbmetall Bor sorgt dafür, dass es auf der Solarzelle positive Ladung gibt. Experten nennen das eine p-leitende Schicht.
"Was geschieht ist, dass das Licht in die Zelle, in das Silizium hineindringt, da Elektronen erzeugt."
Später kommt noch eine Behandlung des Wafer mit Phosphor hinzu, wodurch eine dünne n-leitende Schicht entsteht.
"Die Situation, dass wir ein p-leitendes und ein n-leitendes Gebiet im Silizium haben, sorgt dafür, dass die Zelle negativ und positiv geladen wird, also wenn die Sonne scheint, sich eigentlich wie eine Batterie benimmt. Und dann kann man zum Beispiel eine Lampe anbinden und die brennt dann."
Der Strom aus Solarzellen versorgt neben Lampen auch Parkscheinautomaten, Taschenrechner oder Satelliten und Raumstationen mit dem nötigen Strom. Bevor aus dem schlichten Wafer aber eine spannungsgeladene Solarzelle wird, wird sie geätzt, mit Gasen behandelt und gebrannt.
Bei Solland laufen die Siliziumscheiben auf Bändern durch nahezu vollautomatische Produktionsstraßen - stets gut geschützt durch teils durchsichtige Tunnel. Die Mitarbeiter tragen spezielle Kittel und Handschuhe, damit der Staubanteil in der Luft gering gehalten wird. Menschliche Hände berühren die Wafer aber nie. Die zarten Platten werden nur von überaus flinken Roboterarmen bewegt.
"Der nächste Produktionsschritt wird eine chemische Oberflächenbehandlung sein, die dazu dient, dass die Sonnenzelle kein Licht reflektiert, aber das Licht in sich aufnimmt."
Dazu wird der Wafer chemisch geätzt, so dass eine gleichmäßige, matte Oberfläche entsteht.
"Die Sonnenzelle muss ja Licht in Elektrizität umwandeln, und wenn die Zelle das Licht reflektieren würde, würde das zu einem geringeren Wirkungsgrad führen. Und das wollen wir nicht."
Im Gegenteil. Weltweit wird in Laboren eifrig nach Wegen gesucht, wie die noch relativ geringe Energieausbeute gesteigert werden kann. Mit Erfolg, meint der Solarzellenexperte Henk Koerselmann.
"Die Effizienz der Sonnenzelle, also der Prozentsatz von eingestrahlter Sonnenenergie, die auch wirklich in elektrische Energie umgewandelt wird, dieser Prozentsatz steigt mit etwa 0,5 Prozent pro Jahr."
"Welchen Wirkungsgrad hat denn so eine durchschnittliche Solarzelle, die hier bei Ihnen vom Band läuft?"
"So um die 16 Prozent. Das ist gut."
Damit der Wafer überhaupt irgendwann einmal elektrischen Strom liefert, wird er mit einem feinen Phosphornebel benetzt und läuft dann über eine Bandstraße in einen zwölf Meter langen Ofen. Darin wird das Phosphor bei rund 900 Grad eingebrannt. Anschließend erhält die Solarzelle ihre charakteristische Farbe. Unter Vakuum werden die Zellen mit verschieden Gasen behandelt so dass letztlich eine Schicht aus Siliziumnitrit entsteht. Und diese Schicht ist blau.
"Wir können andere Farben produzieren, wenn wir das wollen. Das geht."
"Sie können rote Solarzellen machen?"
"Ja. Aber die haben dann einen weit geringeren Wirkungsgrad. Also das ist vielleicht schön, aber nicht sehr ökonomisch."
Und ökonomisch muss eine Photovoltaikzelle sein, wenn sie eine zunehmend größere Rolle bei der Energieversorgung spielen soll.
"Es stimmt immer noch, dass ziemlich viel Energie angewendet werden muss, um eine Zelle zu produzieren, aber die Zelle hat eine sehr lange Lebensdauer, 30 Jahre. Und über diese Zeit wird mehrfach die Energie wieder zurückgeholt, die angewendet wurde für die Erzeugung dieser Zelle."
"Kann man da eine ganz konkrete Zahl sagen?"
"In zwei bis drei Jahren wird die Energie wieder zurück gewonnen."
Experten gehen davon aus, dass in den nächsten Jahren nirgendwo auf der Welt so viele Solarstromanlagen installiert werden wie in Deutschland. Und wir sind mit rund 500.000 Photovoltaik-Anlagen schon jetzt Spitzenreiter. Dennoch wird das Potential selbst in Deutschland nicht ansatzweise ausgeschöpft. Das liegt auch an den recht hohen Anschaffungskosten, meint Henk Koerselmann. Immerhin kostet eine Solaranlage für ein Einfamilienhaus zwischen 15- und 20.000 Euro.
Die inzwischen blauen Wafer sind - rein physikalisch - schon eine richtige Solarzelle, in der das Sonnenlicht in elektrischen Strom umgewandelt wird. Doch um den Strom aus der Sonnenzelle gewinnen zu können, müssen noch dünne Silberstreifen und auf der Rückseite eine Aluminiumschicht aufgetragen werden. Sie bilden das Muster, das später auf der fertigen Solarzelle zu sehen ist.
"Und dann ist die Zelle fertig, funktionsbereit."
Draußen, vor der deutsch-niederländischen Fabrik, scheint die Sonne. Wie so oft im vermeintlich schattigen Deutschland. Bestes Wetter für Solarstrom.
Der moderne Flachbau liegt - fast idyllisch zwischen Feldern und Wiesen - genau auf der deutsch-niederländischen Grenze. Ein Teil von "Solland Solar" liegt im deutschen Aachen, der andere im niederländischen Heerlen. Eine blaue Linie quer durch die Fabrik markiert, wo Deutschland endet und die Niederlande beginnen. Rund 40 Prozent der 400 Mitarbeiter haben einen deutschen Pass, die anderen einen niederländischen. So fließt das Wissen aus beiden Ländern in die Entwicklung und Produktion von Solarzellen.
Die Umwandlung von Sonnenlicht in elektrischen Strom beginnt mit einem Material, das es weltweit in nahezu unbegrenztem Ausmaß gibt: Sand. Quarzsand, um genau zu sein, auch Silizium genannt.´
"Silizium in sauberer Form, daraus werden Waferscheiben produziert und die sind Basismaterial für die Fertigung von einer Solarzelle."
Erklärt Henk Koerselmann, der bei Solland für den reibungslosen Produktionsprozess - und die Betreuung von Journalisten - verantwortlich ist. Diese nur 0,2 Millimeter dicken quadratischen Siliziumplatten werden als Rohmaterial eingekauft und tragen bereits eine kleine Menge Bor in sich. Das Halbmetall Bor sorgt dafür, dass es auf der Solarzelle positive Ladung gibt. Experten nennen das eine p-leitende Schicht.
"Was geschieht ist, dass das Licht in die Zelle, in das Silizium hineindringt, da Elektronen erzeugt."
Später kommt noch eine Behandlung des Wafer mit Phosphor hinzu, wodurch eine dünne n-leitende Schicht entsteht.
"Die Situation, dass wir ein p-leitendes und ein n-leitendes Gebiet im Silizium haben, sorgt dafür, dass die Zelle negativ und positiv geladen wird, also wenn die Sonne scheint, sich eigentlich wie eine Batterie benimmt. Und dann kann man zum Beispiel eine Lampe anbinden und die brennt dann."
Der Strom aus Solarzellen versorgt neben Lampen auch Parkscheinautomaten, Taschenrechner oder Satelliten und Raumstationen mit dem nötigen Strom. Bevor aus dem schlichten Wafer aber eine spannungsgeladene Solarzelle wird, wird sie geätzt, mit Gasen behandelt und gebrannt.
Bei Solland laufen die Siliziumscheiben auf Bändern durch nahezu vollautomatische Produktionsstraßen - stets gut geschützt durch teils durchsichtige Tunnel. Die Mitarbeiter tragen spezielle Kittel und Handschuhe, damit der Staubanteil in der Luft gering gehalten wird. Menschliche Hände berühren die Wafer aber nie. Die zarten Platten werden nur von überaus flinken Roboterarmen bewegt.
"Der nächste Produktionsschritt wird eine chemische Oberflächenbehandlung sein, die dazu dient, dass die Sonnenzelle kein Licht reflektiert, aber das Licht in sich aufnimmt."
Dazu wird der Wafer chemisch geätzt, so dass eine gleichmäßige, matte Oberfläche entsteht.
"Die Sonnenzelle muss ja Licht in Elektrizität umwandeln, und wenn die Zelle das Licht reflektieren würde, würde das zu einem geringeren Wirkungsgrad führen. Und das wollen wir nicht."
Im Gegenteil. Weltweit wird in Laboren eifrig nach Wegen gesucht, wie die noch relativ geringe Energieausbeute gesteigert werden kann. Mit Erfolg, meint der Solarzellenexperte Henk Koerselmann.
"Die Effizienz der Sonnenzelle, also der Prozentsatz von eingestrahlter Sonnenenergie, die auch wirklich in elektrische Energie umgewandelt wird, dieser Prozentsatz steigt mit etwa 0,5 Prozent pro Jahr."
"Welchen Wirkungsgrad hat denn so eine durchschnittliche Solarzelle, die hier bei Ihnen vom Band läuft?"
"So um die 16 Prozent. Das ist gut."
Damit der Wafer überhaupt irgendwann einmal elektrischen Strom liefert, wird er mit einem feinen Phosphornebel benetzt und läuft dann über eine Bandstraße in einen zwölf Meter langen Ofen. Darin wird das Phosphor bei rund 900 Grad eingebrannt. Anschließend erhält die Solarzelle ihre charakteristische Farbe. Unter Vakuum werden die Zellen mit verschieden Gasen behandelt so dass letztlich eine Schicht aus Siliziumnitrit entsteht. Und diese Schicht ist blau.
"Wir können andere Farben produzieren, wenn wir das wollen. Das geht."
"Sie können rote Solarzellen machen?"
"Ja. Aber die haben dann einen weit geringeren Wirkungsgrad. Also das ist vielleicht schön, aber nicht sehr ökonomisch."
Und ökonomisch muss eine Photovoltaikzelle sein, wenn sie eine zunehmend größere Rolle bei der Energieversorgung spielen soll.
"Es stimmt immer noch, dass ziemlich viel Energie angewendet werden muss, um eine Zelle zu produzieren, aber die Zelle hat eine sehr lange Lebensdauer, 30 Jahre. Und über diese Zeit wird mehrfach die Energie wieder zurückgeholt, die angewendet wurde für die Erzeugung dieser Zelle."
"Kann man da eine ganz konkrete Zahl sagen?"
"In zwei bis drei Jahren wird die Energie wieder zurück gewonnen."
Experten gehen davon aus, dass in den nächsten Jahren nirgendwo auf der Welt so viele Solarstromanlagen installiert werden wie in Deutschland. Und wir sind mit rund 500.000 Photovoltaik-Anlagen schon jetzt Spitzenreiter. Dennoch wird das Potential selbst in Deutschland nicht ansatzweise ausgeschöpft. Das liegt auch an den recht hohen Anschaffungskosten, meint Henk Koerselmann. Immerhin kostet eine Solaranlage für ein Einfamilienhaus zwischen 15- und 20.000 Euro.
Die inzwischen blauen Wafer sind - rein physikalisch - schon eine richtige Solarzelle, in der das Sonnenlicht in elektrischen Strom umgewandelt wird. Doch um den Strom aus der Sonnenzelle gewinnen zu können, müssen noch dünne Silberstreifen und auf der Rückseite eine Aluminiumschicht aufgetragen werden. Sie bilden das Muster, das später auf der fertigen Solarzelle zu sehen ist.
"Und dann ist die Zelle fertig, funktionsbereit."
Draußen, vor der deutsch-niederländischen Fabrik, scheint die Sonne. Wie so oft im vermeintlich schattigen Deutschland. Bestes Wetter für Solarstrom.
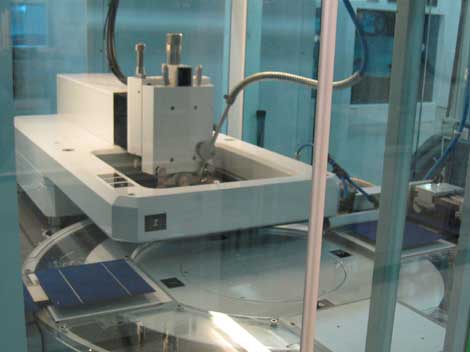
Solarzellenproduktion bei der deutsch-niederländischen Firma Solland Solar.© Stephanie Kowalewski